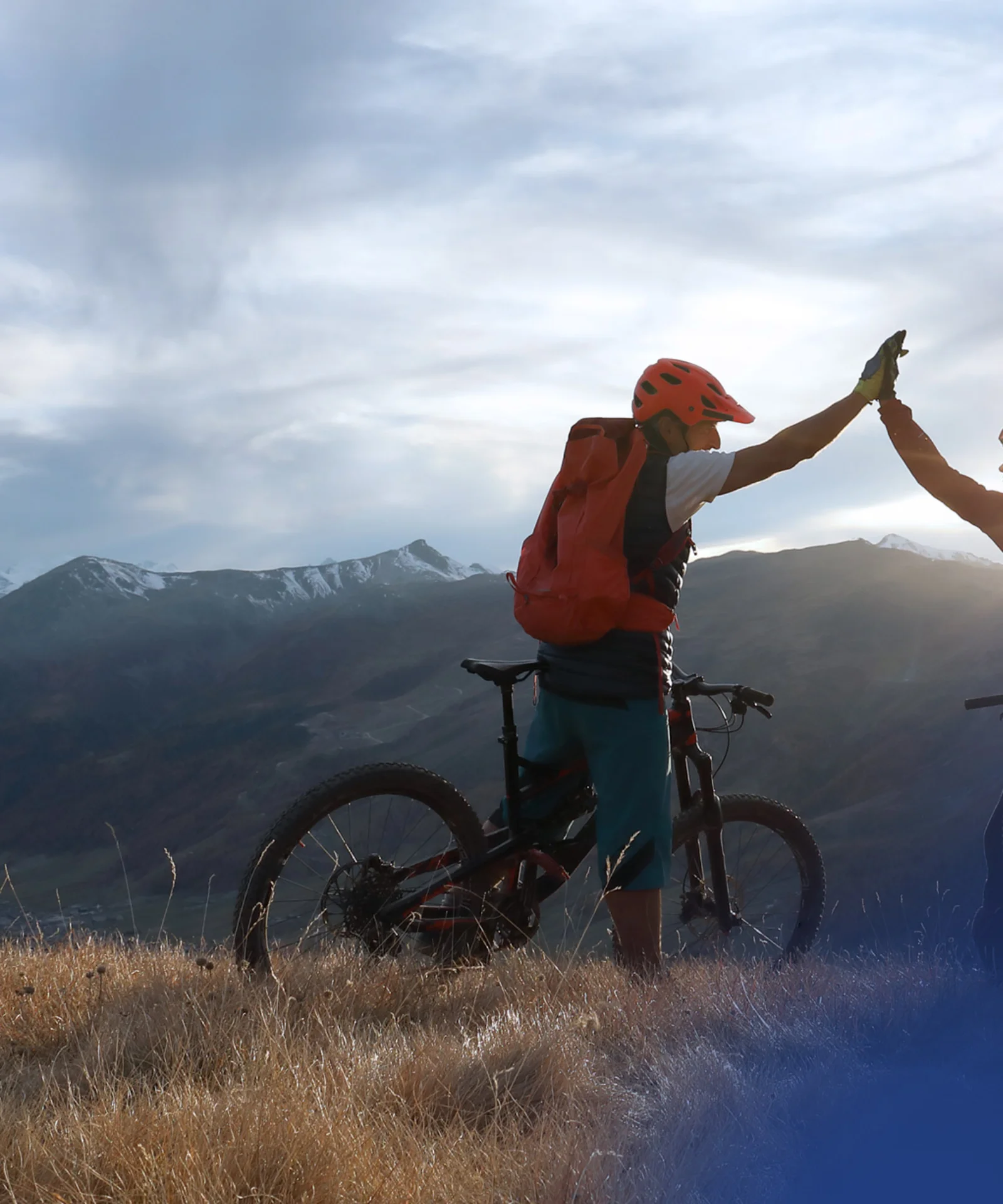
GFT erwirbt Sophos Solutions von Advent International
GFT erweitert mit der Akquisition von Sophos Solutions Kernbankenkompetenz und Kundenstamm, sowie globale Präsenz und Team um fast 20%.
Mehr erfahren
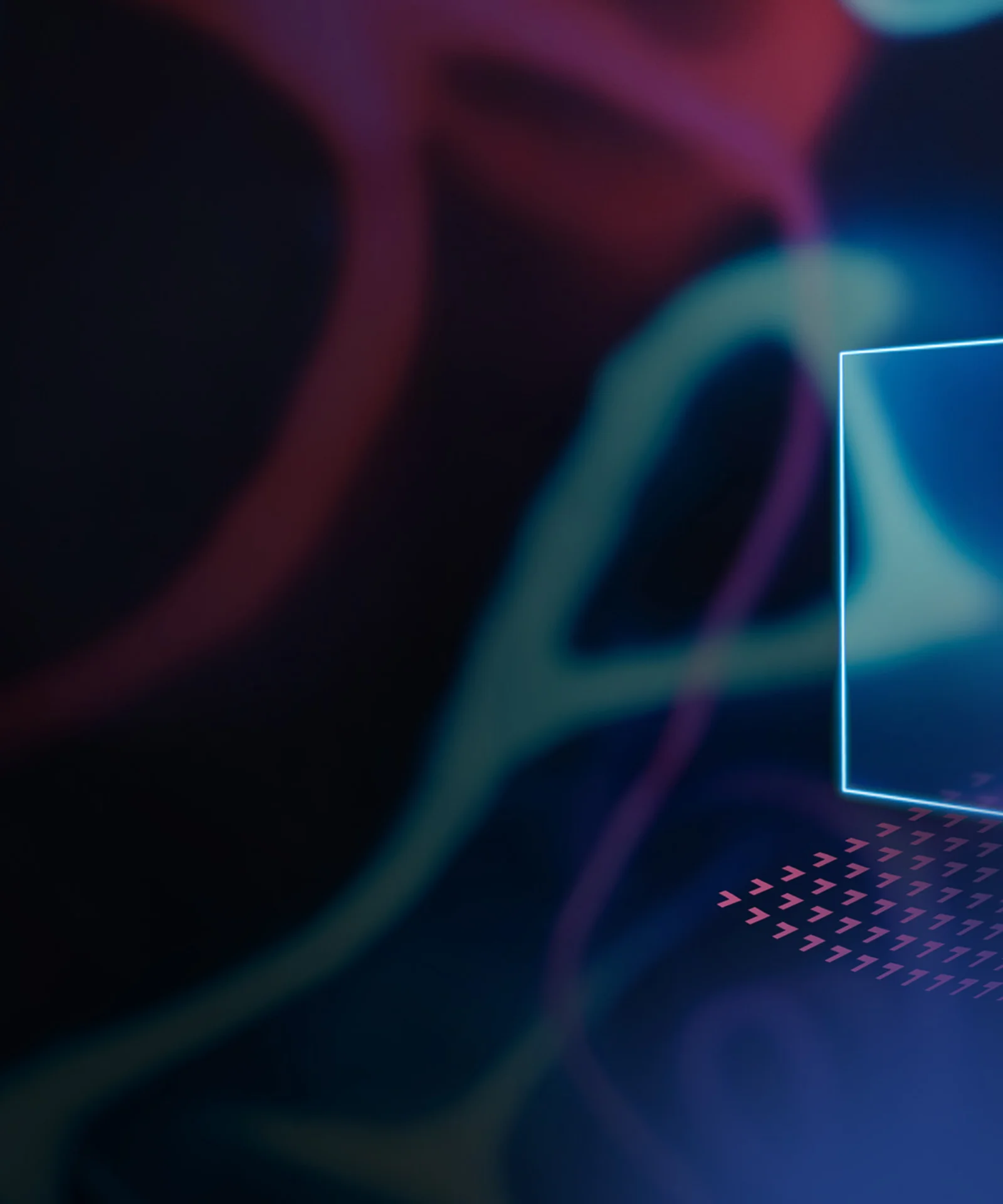
Schneller zu Ihrer KI Lösung
Den Unternehmenswert steigern mit KI und Daten.
Schnell. Sicher. Effizient.
Mehr erfahren
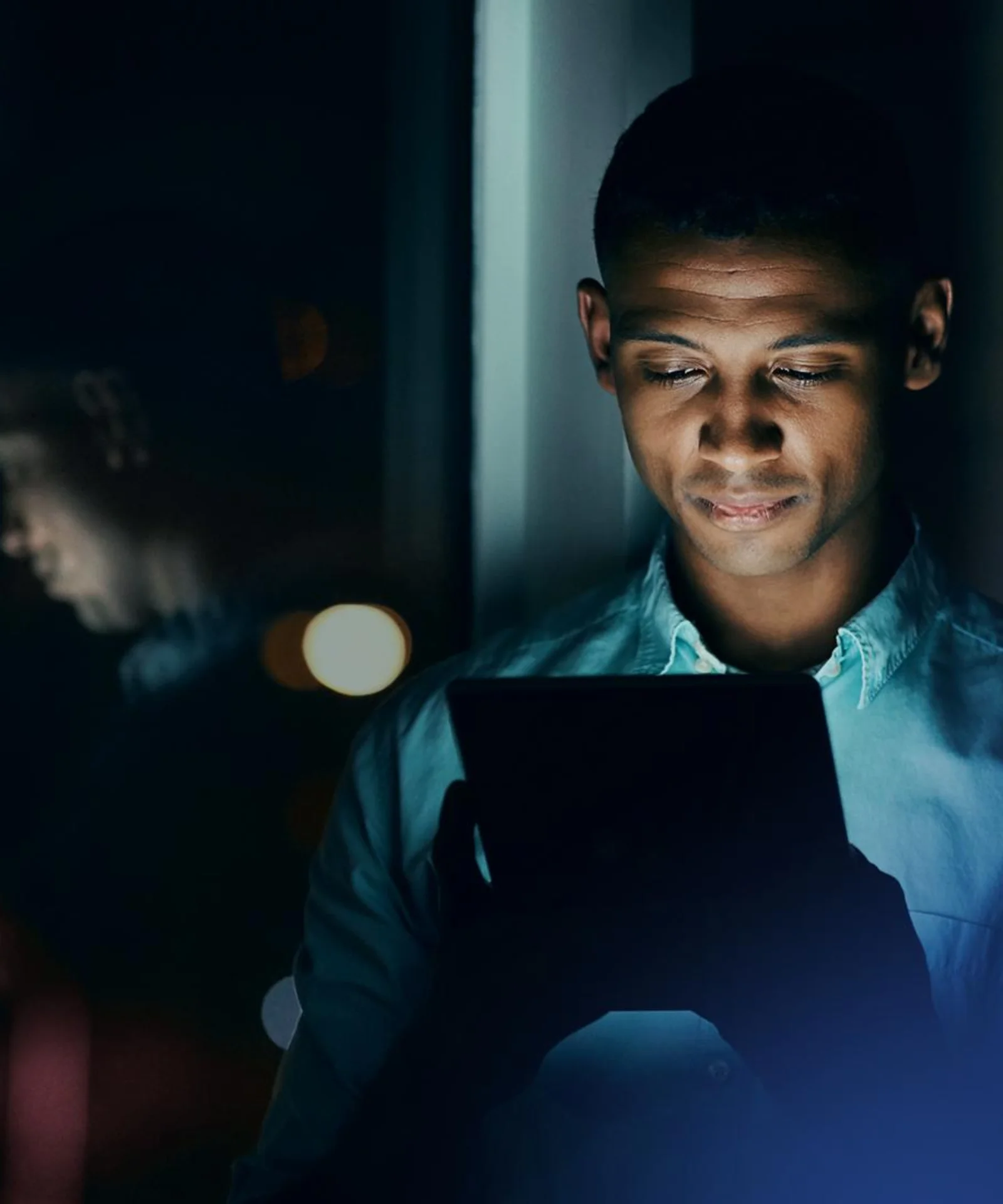
Liliana Scheck wird CEO der GFT Schweiz
Managerin will Nachhaltigkeit und Wachstum bei Kunden durch digitale Technologien fördern
Mehr erfahren
starkes Partner Ökosystem