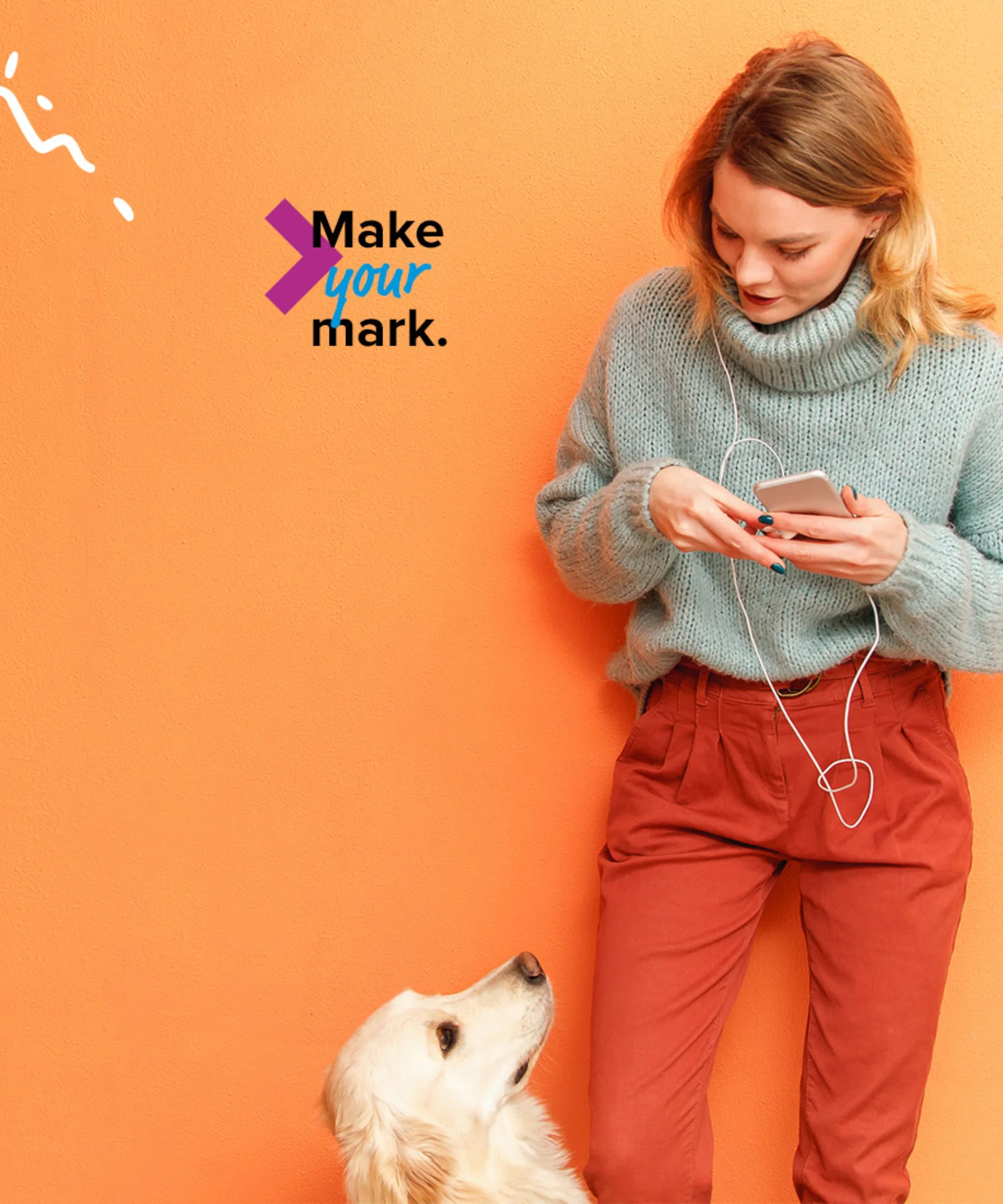
Your career at GFT
At GFT, everyone has the opportunity to live out their strengths, drive new ideas, and create value as an individual or part of a team. Let's set an example together.
Show more
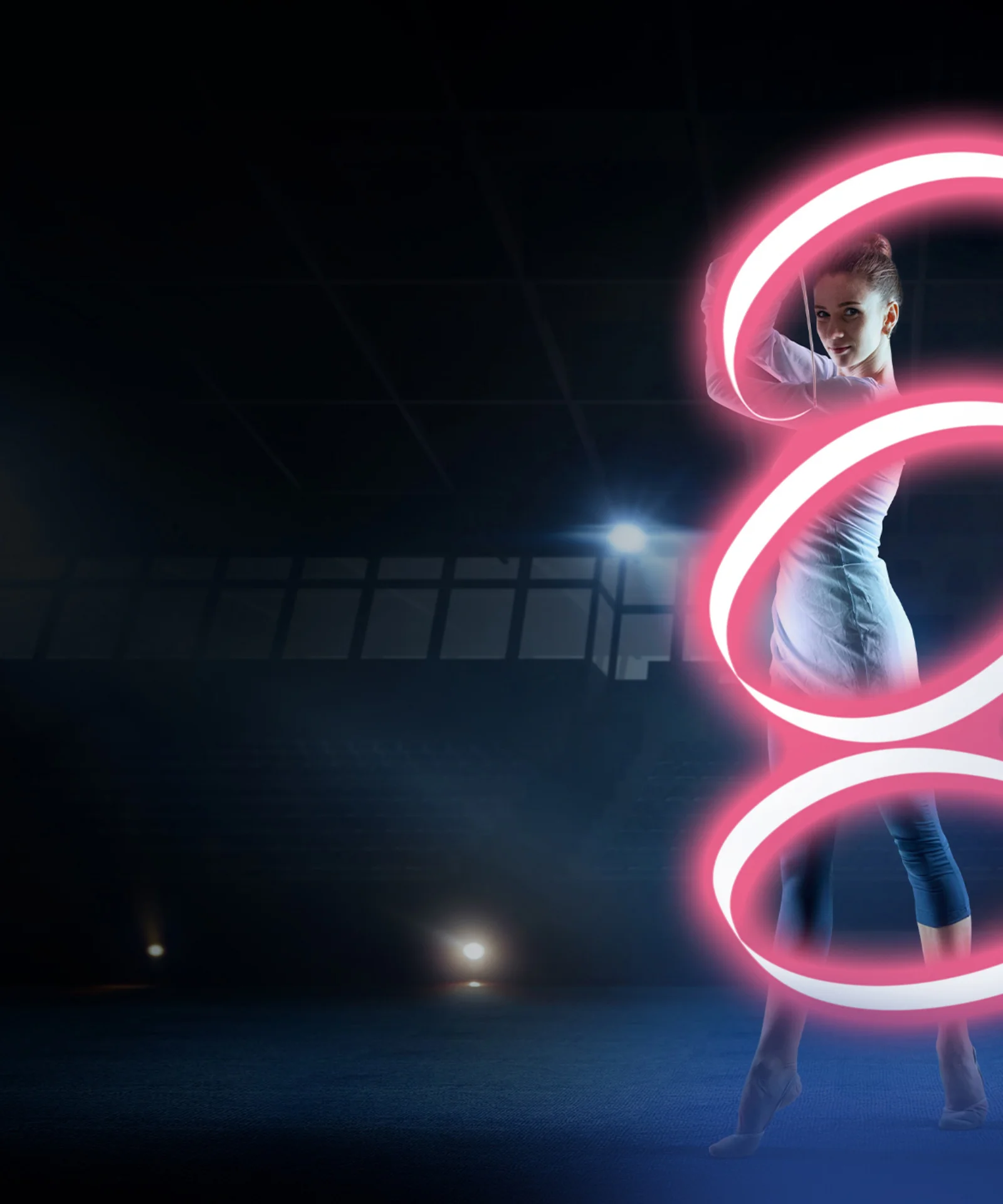
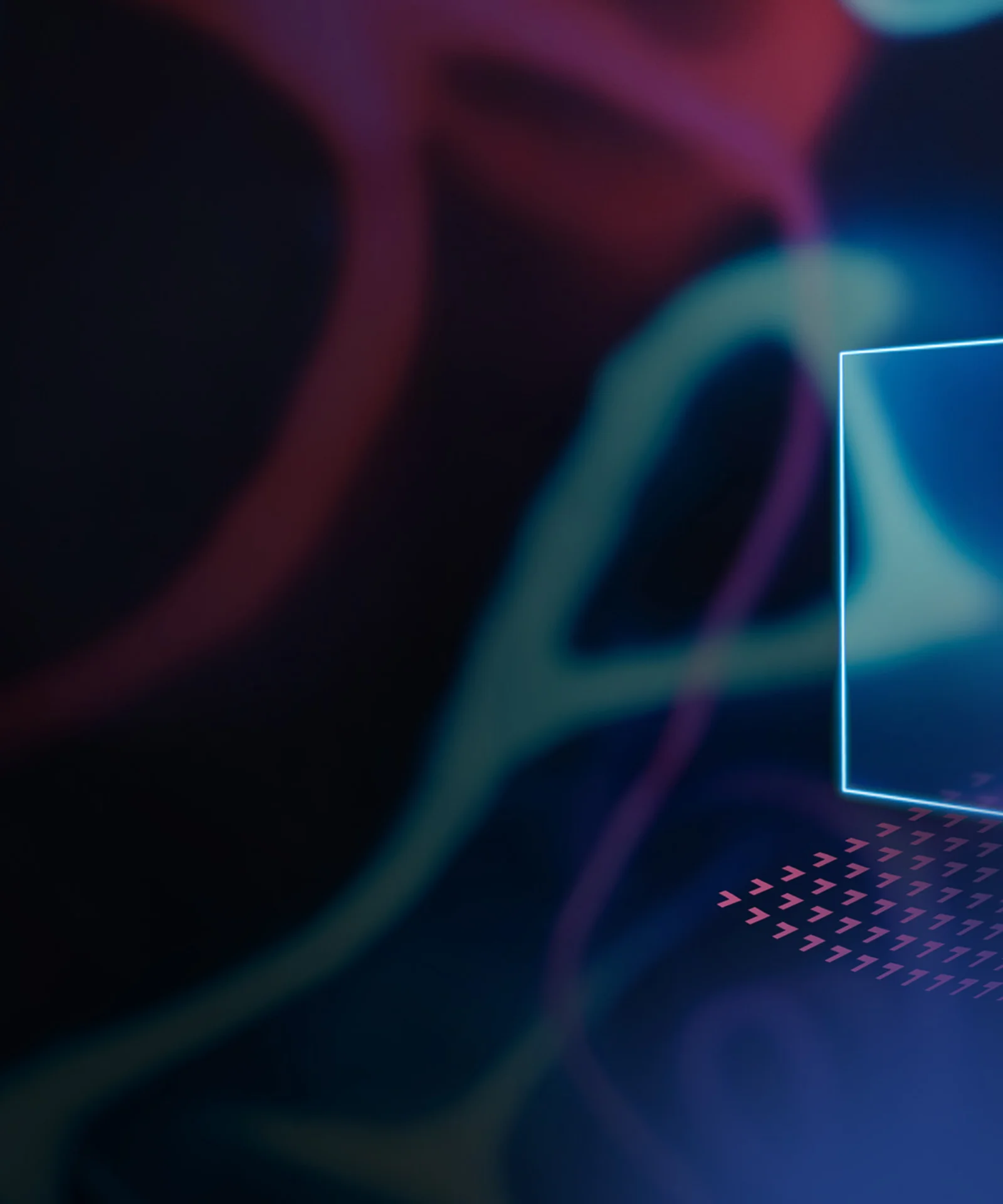
Fast track to AI:
GFT AI.DA Marketplace
Creating business value with AI and data.
Fast. Secure. Efficient.
Show more
Fast. Secure. Efficient.
Strong partner ecosystem