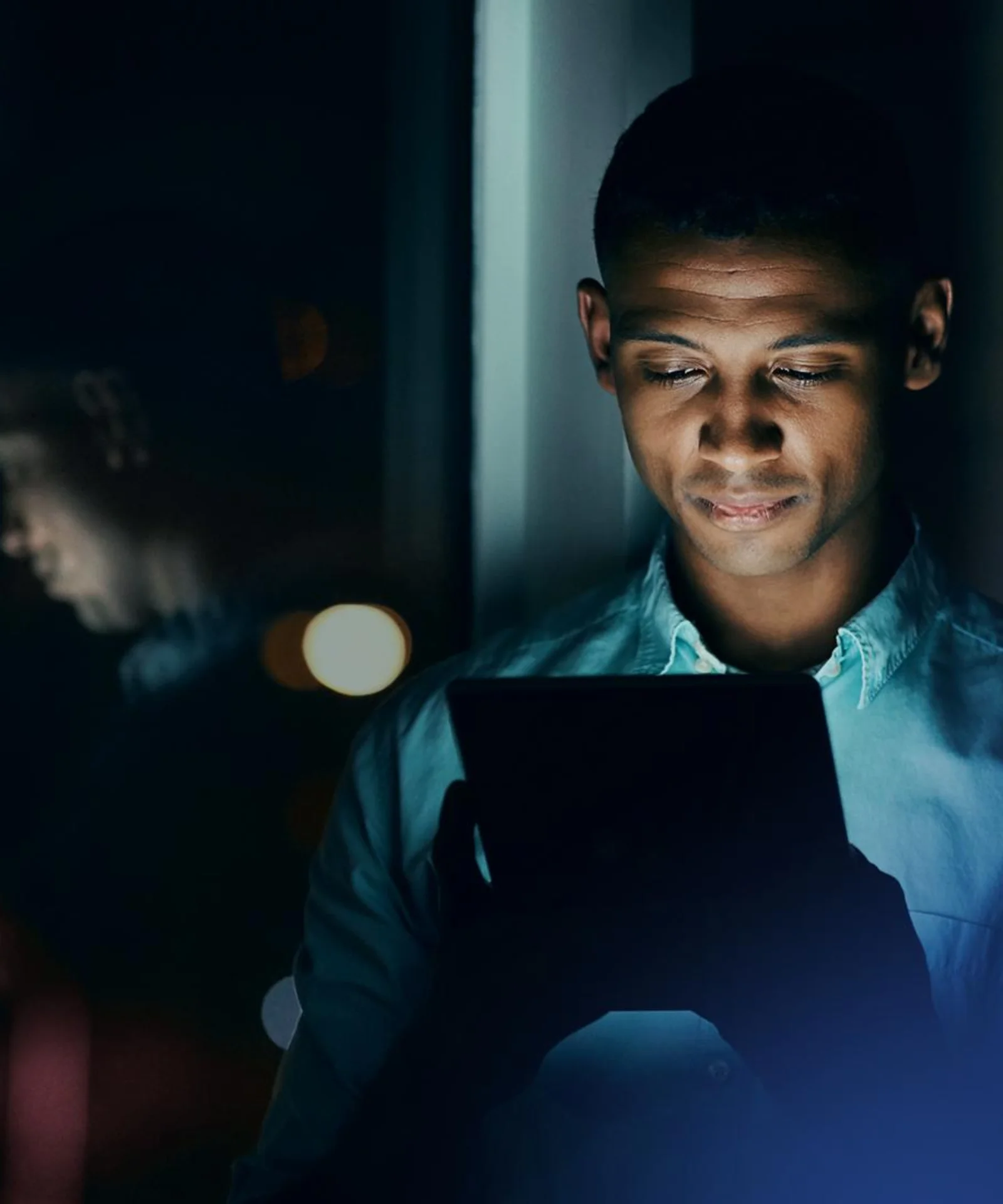
Marco Santos to become CEO of GFT Technologies SE
CRFO Jochen Ruetz additionnaly to become Deputy CEO
Show more
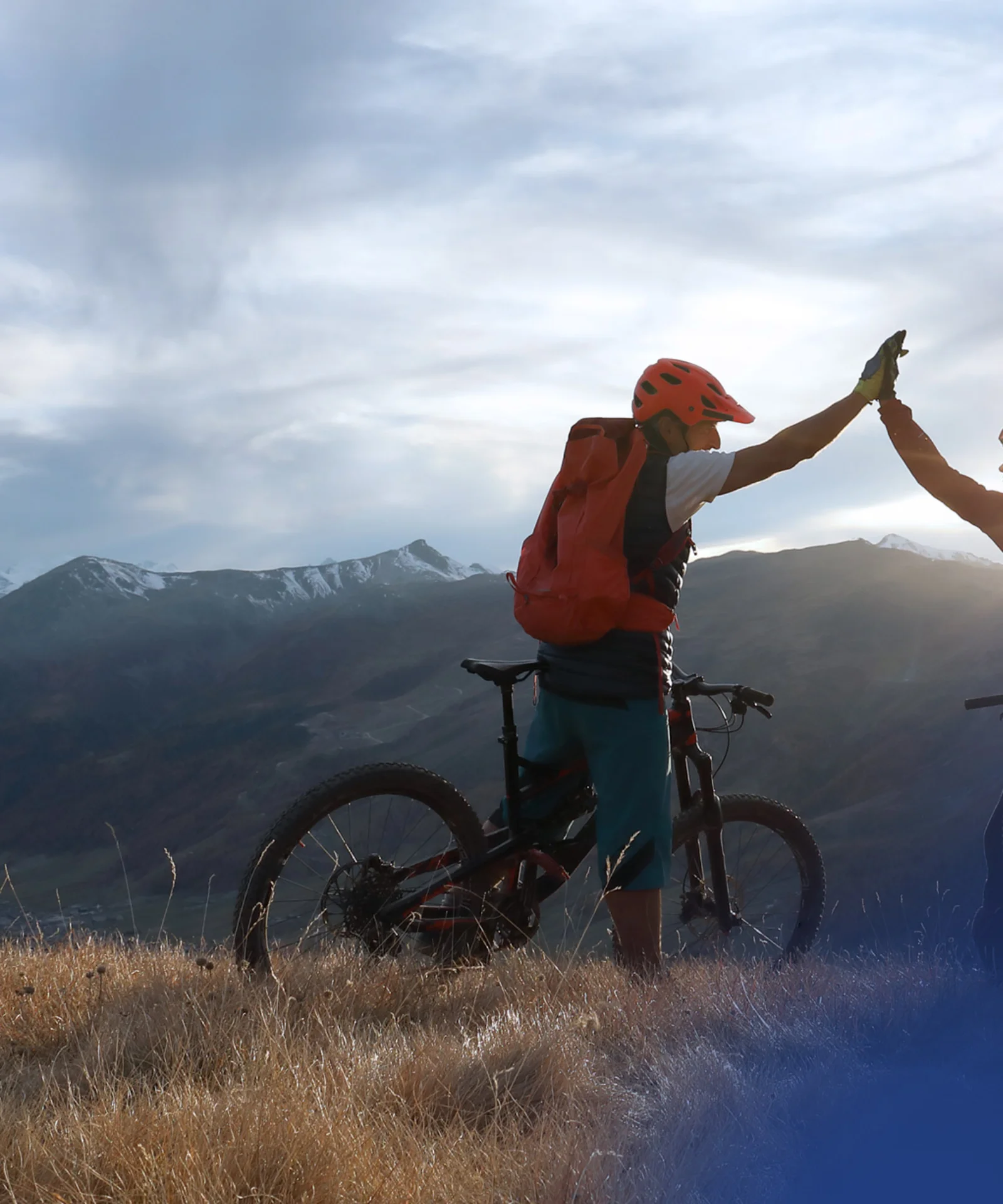
GFT acquires Sophos Solutions from Advent International
With the acquisition of Sophos Solutions, GFT expands core banking expertise and client base, also footprint and team by almost 20%.
Show more
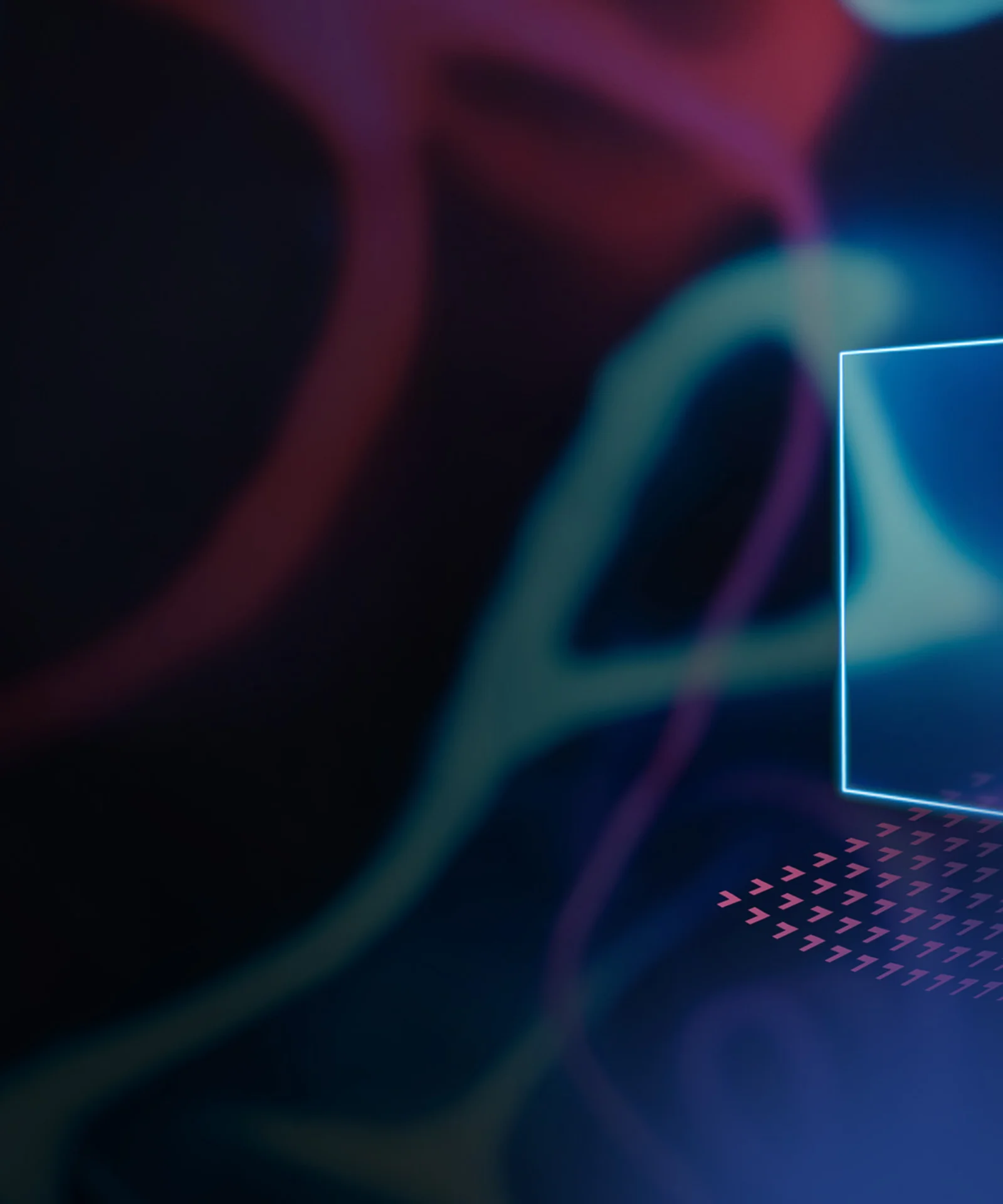
Fast track to AI:
GFT AI.DA Marketplace
Creating business value with AI and data.
Fast. Secure. Efficient.
Show more
Fast. Secure. Efficient.

Shifting gears in
software development:
GFT AI Impact Beta
Imagine you could tackle the most common challenges in one go.
Show more
Strong partner ecosystem